CNC Machining Magnesium
Computer numerical control, or CNC, machine cutting is a versatile and precise manufacturing method. The material must be extracted from a workpiece using computer-controlled equipment to create complex and precise components. CNC machining often uses magnesium as a material. Due to its numerous advantages, including its low density, high strength-to-weight ratio, and superior thermal conductivity, magnesium is perfect for various applications. However, there are specific challenges and factors to consider while grinding magnesium. The pros and cons of CNC machining magnesium will be covered in this article. You will be knowing more about it through reading .
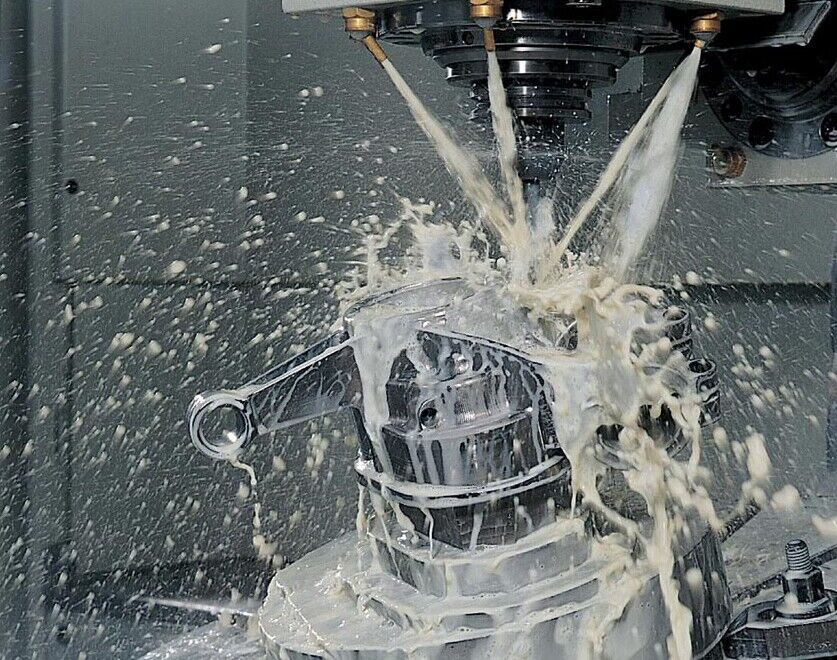
Advantages of Machining Magnesium
Magnesium is a highly sought-after material in many sectors since it can be machined and has several benefits. We examine the main benefits of machining magnesium below:
1. Low Density: Magnesium is one of the lightest structural metals on the market because of its renownedly low density. This quality is beneficial in situations where weight loss is the main priority. Magnesium has advantages in the aerospace and automotive industries because it may decrease component weight without compromising strength or performance.
2. High Strength-to-Weight Ratio: This quality is beneficial when components must endure mechanical forces and strains. Engineers may significantly reduce weight while retaining structural integrity by using magnesium.
3. Superior Thermal Conductivity: Magnesium is an excellent thermal conductor essential for applications requiring heat dissipation. It is the perfect option for electrical enclosures and cooling components because it can transmit heat effectively. Due to its excellent thermal conductivity, magnesium prolongs the life of delicate electronic equipment and helps avoid overheating.
4. Machinability: Magnesium has excellent machinability, which is a big plus for the industry. Due to its comparatively low cutting resistance, it can be machined effectively and precisely, reducing machining times and manufacturing costs. Magnesium is a desirable alternative for many sectors because manufacturers can quickly build complicated, tight-tolerance components.
5. Less Vibration: The dampening qualities of magnesium contribute to less vibration during machining, resulting in a more stable and predictable production process.
6. Magnesium is readily recyclable, which promotes sustainability and environmental stewardship. Magnesium recycling uses much less energy than initial manufacturing, making it a sustainable option. This characteristic supports the growing focus on sustainability in contemporary production techniques.
7. Ergonomics and Handheld Devices: The lightweight nature of magnesium makes it helpful in making tools and other portable electronics. The material’s lighter weight enhances user comfort and lessens operator fatigue during extended usage. Magnesium may be used in power tools, cameras, computers, cellphones, and other electronic devices to improve user experience.
8. High Specific Stiffness: Specific stiffness measures how stiff a substance is to its weight. Magnesium alloys are a popular option for applications that need strength and lightweight construction due to their outstanding specific stiffness. This quality is crucial in industries like aircraft, where every ounce saved translates into better fuel economy and cargo capacity.
Challenges of Machining Magnesium
Despite its many benefits, machining magnesium poses unique difficulties that need careful thought and efficient mitigation techniques. The following are these difficulties:
- Flammability: Magnesium’s high flammability is one of the biggest obstacles to machining. During milling, magnesium particles and dust might catch fire. This creates a significant fire risk, necessitating strict fire safety precautions, including Class D fire extinguishers, fire-resistant cutting fluids, and enclosed machining facilities. Operators must get thorough training in fire safety procedures.
- Corrosion Susceptibility: Magnesium is prone to corrosion, particularly in humid or salty situations. Components made of machined magnesium may rapidly deteriorate if not adequately protected. It is usual to use post-machining techniques like anodizing, painting, or surface treatments to increase corrosion resistance. Storage and handling must also be carefully considered to avoid coming into contact with corrosive materials.
- Tool Wear:The abrasive nature of magnesium might result in increased tool wear. Cutting tool selection is critical, and because of their durability, materials like carbide or polycrystalline diamond (PCD) are chosen.
- Chip control: It’s crucial to handle magnesium machining chips effectively. Chips must be adequately removed from the work area due to their flammability to avoid fires. High-pressure air or vacuum systems are often used to quickly and securely remove chips. Additionally, chip length and flammability may be reduced using toolpath procedures that use chip-breaking processes.
- Surface Finish: Due to magnesium’s reactivity with air, achieving a high-quality surface finish may be difficult. Magnesium is easily oxidized, and this may lead to surface flaws. Toolpath methods that reduce tool contact and specialized cutting fluids created for magnesium machining may be used to improve surface finish quality. Climb milling is often advised to reduce friction and enhance surface smoothness.
- Workholding and Setup: To machine magnesium components precisely, a solid setup and reliable clamping are required. Surface imperfections and decreased precision may result from vibrations during milling. To minimize this problem, working solid techniques and a well-balanced setup are essential.
- Speed and Feed Rates:To avoid overheating and reduce tool wear, optimizing cutting parameters, such as spindle speed and feed rates, is crucial. To strike the ideal balance between productivity and tool life, start with conservative settings and progressively increase them as you acquire expertise with specific machining configurations.
Tips for CNC Machining Magnesium
Consider the following advice to overcome the difficulties in machining magnesium:
Fire Safety Measures
- Use chip guards and enclosures to confine the chips and stop them from spreading.
- Routinely clear the machining area of dust and chip accumulation.
Tool Selection Techniques:
- Select tools composed of materials like carbide or polycrystalline diamond (PCD) that are resistant to adhesion and wear.
- To optimize performance and tool life, use coated tools made of aluminium titanium nitride (AlTiN) or titanium nitride (TiN).
Lubricant and coolant:
- To decrease heat and prolong tool life, use specific cutting fluids made for magnesium machining.
- Ensure a steady coolant flow to help with chip evaporation and temperature regulation.
Chip management:
- Use effective chip evacuation techniques, such as high-pressure air or vacuum systems, to clear the workspace of chips.
- Encourage toolpath programmers to utilize appropriate chip-breaking methods to shorten chips and reduce their flammability.
Prevention of Corrosion
- To improve corrosion resistance, consider post-machining procedures such as anodizing, painting, or other surface treatments.
- Prevent exposure to moisture and corrosive materials by carefully handling and storing magnesium components.
Setup and Workholding:
- To reduce vibrations during machining, which might result in surface flaws, use reliable workholding techniques.
- Ensure your setup is well-balanced and clamped securely to prevent tool chatter and get precise results.
Feed rates and speed:
- To avoid overheating and tool wear, optimize cutting parameters such as spindle speed and feed rates.
- As you get familiar with your particular machining setup, start with cautious speeds and feeds and progressively raise them.
Surface Quality:
- Utilize climb milling whenever you can to lessen the tool’s propensity to rub against the material, which produces a smoother surface finish.
- Experiment with different toolpath tactics to reduce tool engagement and enhance surface finish quality.
Conclusion
Due to the material’s unique characteristics, such as its low density and high strength-to-weight ratio, CNC machining magnesium may be a fruitful venture. To guarantee safety and achieve accuracy, knowing the related problems and taking the necessary steps is crucial.
You may more successfully overcome the difficulties of machining magnesium by using the advice provided in this manual. To improve the safety and effectiveness of your machining operations, remember to prioritize fire safety, use the appropriate equipment, control chips, and optimize cutting settings. Magnesium may be a valuable material for various applications across industries with the correct approach.