The automobile business is no stranger to innovation and technological breakthroughs, and one area that has seen substantial growth in recent years is the creation and manufacture of metal components. The rapid prototyping technique has emerged as a game-changer, transforming how automobile metal components are developed, tested, and produced. This article discusses rapid prototyping technology’s influence on the automobile industry, with a particular emphasis on the advantages, practical uses, and untapped potential of this technology.
The Basics of Rapid Prototyping
Rapid prototyping is a manufacturing technique that builds three-dimensional items layer by layer from digital drawings. Rapid prototyping constructs objects by gradually adding material, unlike conventional manufacturing techniques, which often require subtractive operations like cutting or milling. The potential of this technology to manufacture complicated geometries with shorter lead times and lower prices has dramatically increased its appeal.
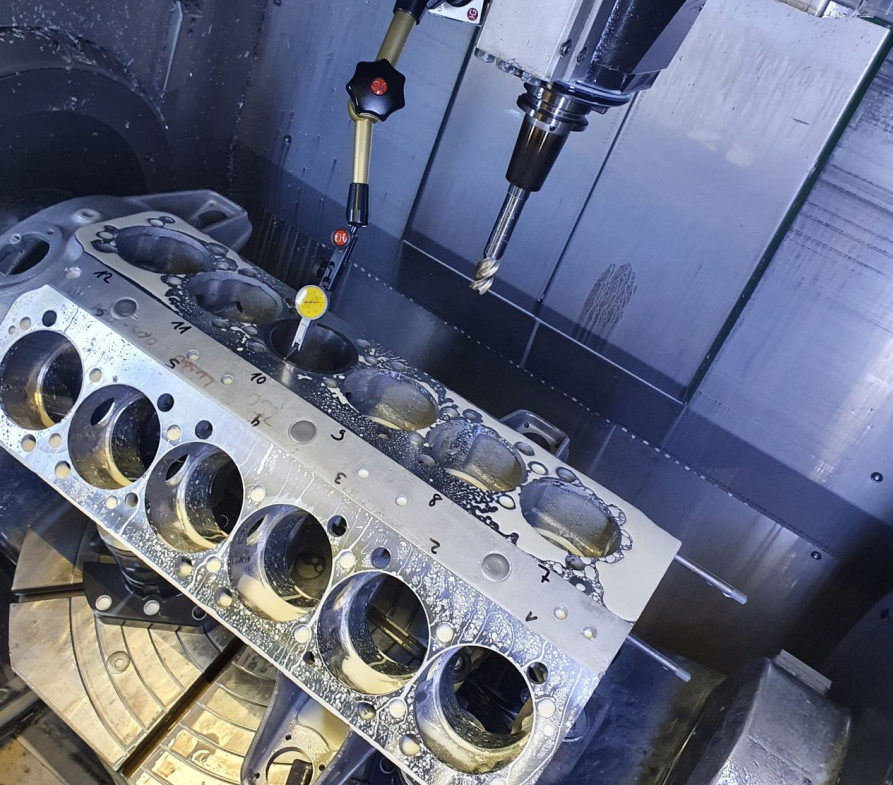
Key Benefits of Rapid Prototyping:
Accelerated Design Iterations
Thanks to rapid prototyping services, automotive engineers and designers can iterate and improve their concepts. They can quickly create actual prototypes rather than depending just on digital ones. Because of the rapid turnaround time, design iterations may be completed more quickly, allowing for the early detection and correction of design defects or functional concerns. As a result, automotive businesses may drastically shorten the time needed to introduce new goods or components to the market, enabling quicker innovation and product development cycles.
Cost Reduction
Traditional manufacturing processes can require significant up-front expenditures, such as setup and tooling costs. For complicated metal items, these expenses may be highly significant. Because components are constructed layer by layer directly from digital blueprints, rapid prototyping removes the need for costly tooling, molds, and dies. By doing this, the necessity for time-consuming and expensive tooling operations is removed. Consequently, automobile businesses may save much money, particularly on low-volume manufacturing, bespoke parts, and limited production runs.
Flexibility and Complexity of Design
For automobile designers, rapid prototyping technology provides unmatched design freedom and flexibility. It makes it feasible to produce elaborate and complicated geometries that were previously difficult or perhaps impossible to fabricate. By employing lightweight constructions and complex internal geometries, designers may improve component performance, decrease weight, and increase fuel economy. This degree of design intricacy may enhance the overall functioning and visual appeal of vehicle components.
Faster Time-to-Market
Rapid prototyping considerably speeds up the time-to-market for new automotive goods by simplifying the design and production processes. Quick physical prototype production allows designers to test their work, get user input, and iterate the design as needed. Companies may release new models, enhancements, or upgrades to current goods more quickly because of this expedited product development cycle. Faster product release speeds up competition and guarantees that automakers remain ahead of the curve in a continually changing market.
Improved Collaboration and Communication
Rapid prototyping makes better cooperation and communication between the numerous stakeholders involved in the automobile design and production process possible. Teams can see and physically analyze ideas, provide input, and make defensible choices when physical prototypes are easily accessible. Better product outputs result from this collaborative approach’s reduction of misconceptions, mistakes, and ineffective communication.
Applications of Rapid Prototyping in the Automotive Industry
Visualization and Conceptual Design
Rapid prototyping allows Automotive designers to turn their creative concepts into tangible models. Designers may assess the proposed design’s aesthetics, ergonomics, and overall appearance and feel by turning computer concepts into physical prototypes. Early in the product development cycle, this visualization capability aids stakeholders, including designers, engineers, and executives, in better understanding and validating the design idea.
Testing and Functional Prototyping
Functional prototyping and testing is one of the critical uses of rapid prototyping in the automobile industry. These prototypes may be used to assess metal components’ functioning, performance, and fit. Engineers may find and fix possible design faults, improve performance, and ensure the finished product complies with the requirements and quality standards by thoroughly testing the prototypes.
Manufacturing and Customization of Spare Parts
Manufacturing spare parts for out-of-production or older model cars presents difficulties for the automobile industry. Rapid prototyping provides a workable option by allowing for the fabrication of metal components on demand. Automotive firms no longer need to keep a massive inventory since the digital design files are easily accessible and can be used to make replacement components as and when they are required. Rapid prototyping also enables component modification to fit particular needs, such as adjusting to various vehicle types or accommodating design changes.
Production of Tooling and Fixtures
The development of fixtures and tooling needed in manufacturing automobiles also uses rapid prototyping technologies. Rapid prototyping methods enable the economical production of complex and specialized tooling, such as jigs, fixtures, and molds. This enables quicker tool development, lower costs, and increased production effectiveness. Rapid prototyping also makes it possible to create tooling designs that are both lightweight and optimized, which may improve manufacturing procedures as a whole.
Communication and Design Validation
Rapid prototyping is a valuable technique for confirming and disseminating design concepts within the automobile sector. Engineers and designers may conduct design reviews, get input, and produce the required design revisions using physical prototypes. By detecting and correcting design concerns early on, this iterative method lowers the likelihood of mistakes and raises the design standard. Furthermore, by offering a concrete representation of the proposed design, physical prototypes promote improved communication with stakeholders, such as customers, suppliers, and production teams.
Future Potential and Advancements in Rapid Prototyping
Materials Innovation
The creation of novel materials designed expressly for rapid prototyping is on the horizon. The development of advanced metal alloys, composites, and hybrid materials is ongoing to fulfill the stringent demands of the automobile industry, particularly those for strength, heat resistance, and durability.
Large-Scale Manufacturing
Although small-scale production has been the primary use for rapid prototyping, there are now initiatives to scale up the technique for large-scale manufacturing. Rapid prototyping for mass manufacturing of metal components in the automobile sector is being accelerated by advancements in printing speed, build size, and automation.
Integration with Digitalization and AI
Artificial intelligence (AI) and digitalization may be used with rapid prototyping technologies to provide a more streamlined and effective manufacturing process. Digital twins can mimic and evaluate component performance before physical manufacture, while AI algorithms may optimize designs for weight savings or structural integrity.
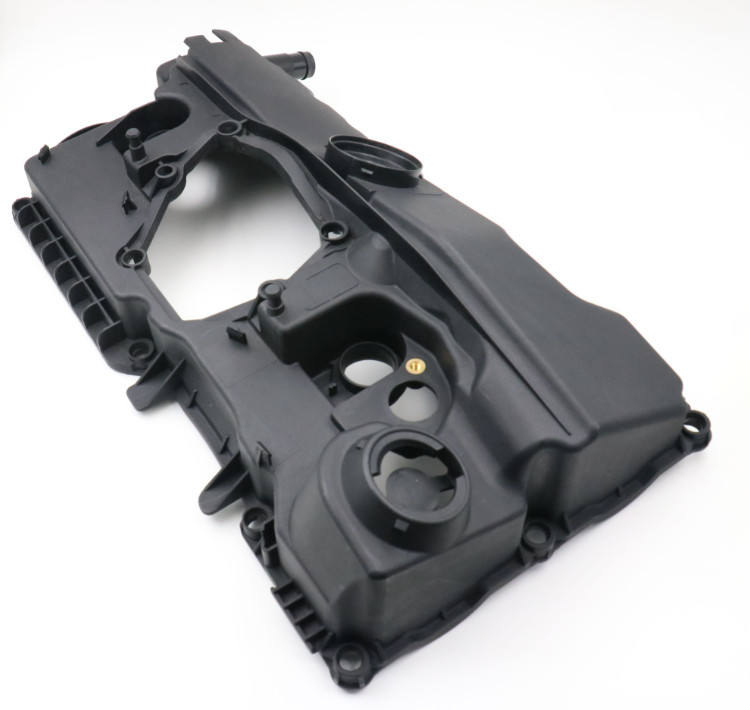
Conclusion
Rapid prototyping technologies in designing, testing, and producing metal components are changing the automobile sector. It is a vital tool for automotive firms aiming for innovation and efficiency because of its advantages, including rapid design iterations, cost savings, design flexibility, and complexity. Rapid prototyping has already substantially influenced the industry, with applications spanning from conceptual design and functional prototyping to spare part manufacture and customization. Looking forward, rapid prototyping has the potential to be used in large-scale production, the integration of digitalization, and artificial intelligence. This technology will likely be essential in determining how metal parts manufacturing in the automobile industry will develop as it develops.