HOW TO MAKE A PLASTIC PROTOTYPE
There are main five technologies making plastic prototype as following:
SLA rapid prototyping
SLA technology, it’s early plastic rapid prototyping method in last century, it changed the industry development and direction. Improved human beings of production Today Application of automobile body manufacturing SLA technology can produce the required proportion of precision casting abrasive, which cast a certain proportion of the body metal model, the use of this metal model can be wind tunnel and collision test, to complete the final evaluation of the body To determine whether the design is reasonable. Chrysler has made use of SLA technology body model, put it in high-speed wind tunnel for aerodynamic test analysis, and achieved satisfactory results, significant savings in the cost of the trial.
SLS rapid prototyping
SLS technology and SLA technology is very similar, but with the powder raw material to replace the liquid photopolymer, and a certain scanning speed and energy on the powder material. The technology has a wide selection of raw materials, easy to clean up the excess material, a wide range of applications Advantages, suitable for the manufacture of prototypes and functional parts. In the forming process, the laser operating parameters and the characteristics of the powder and the sintering atmosphere is an important parameter affecting the quality of sintering. The use of SLS technology from the Texas State University in the manufacture of automotive molds has been commercialized by the United States of America D TM. At present the company has developed the third generation of SLS2000 series of products. The system can sinter wax, polycarbonate, nylon, gold And other materials. With the system made of steel and copper alloy injection mold, can be molded 50,000 pieces of workpieces. In recent years based on RPM technology mold manufacturing technology from the original prototype manufacturing, development to rapid tooling manufacturing, become a domestic and foreign application research and development.
The key of RPM-based mold manufacturing methods can be divided into direct molding method and indirect tooling method. Direct mold method is directly used to produce mold RPM technology, in the RPM technology can be directly produced by the metal mold is the SLS method. In this way, the manufacture of steel copper alloy injection mold, life of up to 50,000 or more. But this method in the sintering process The material in the larger contraction, the accuracy is difficult to control.
3D printing prototype
There are 3 main steps in 3D printing:
The first step is to prepare before printing, where you design a 3D file of the object that you want to print. This 3D file can be created with a CAD software, scanned with a 3D scanner, or simply downloaded from an online market place. After you have verified that your 3D file is printable, you can proceed with the second step.
The second step is the actual printing process. First, choose the material, preferably based on the specific properties that your object needs. The variety of materials used in 3D printing is very wide. It includes plastic, ceramics, resin, metal, sand, textiles, biomaterials, glass, food and even moon dust! Most of these materials also allow you to make a finish to get the exact design result you’ve imagined. Others, such as glass, are still in development and are less accessible.
The third step is the finish. This step requires specific skills and materials. When the object is first printed, it can often not be used directly or delivered before it is sanded, dyed or painted. The selected material usually determines the printing process.
Plastic Prototype CNC Machining
Historically metals have always been fashioned and milled for parts and production. Recently plastics have become a preferred alternative for metals in a variety of industries so there has been an increase in the need for CNC Machining plastic prototype service. Computer numerical control (CNC) utilizes computer programs to control machining processes. Benefits of Using CNC to Machine Plastics, CNC plastic machining is an imperative part of getting exact dimensions for the following project scopes.
Surface Finish – After machining takes place, plastic has a superior surface texture when compared with other processes. The component has a clean and smooth look when professionally machined.
Consistent Quality Production – CNC Plastic machining allows for tight control over product specifications to make sure they are consistent whether large or small production orders.
Complex Geometry – CNC plastic machining offers one of the best ways to create sophisticated niches and angles.
Industry Friendly – Plastic is becoming a popular material for many industries such as energy, aerospace, electrical, electronics, and optical.
Cost savings – When it comes to manufacturing costs, it is very often less expensive to machine plastic parts rather than use other processes such as injection molding. The cost of the tooling can be very expensive and require extremely large production runs to recover the cost.
Vacuum Casting
Vacuum casting is a follow-up procedure used in conjunction with a pattern model and a silicone molding that allows us to produce polyurethane castings models quickly and affordably. Depending on the complexity of the prototype plastic parts 15 to 25 pieces can be created using one silicone molding. A silicone moulding is placed inside a vacuum chamber and is filled with polyurethane through a feed channel. During this process, the vacuum sucks out any air trapped inside the silicone moulding, thus making sure that no air bubbles form in the finished prototype. This allows the production of high-quality, complex prototypes for numerous purposes such as functionality tests, fittings or near series tests.
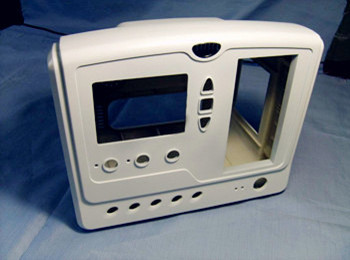