CNC machining for manufacturing complex parts
The industrial sector has revolutionized thanks to the development of highly accurate and efficient CNC (Computer Numerical Control) machining. Due to this technology, manufacturing times have been significantly cut, accuracy has increased, and design flexibility has increased. We’ll go over the main procedures from design and programming to machining and finishing. Comprehending these methods will give you helpful information about using CNC machining to produce complex, high-quality components.
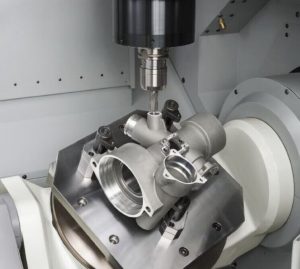
The industrial sector has revolutionized thanks to the development of highly accurate and efficient CNC (Computer Numerical Control) machining. Due to this technology, manufacturing times have been significantly cut, accuracy has increased, and design flexibility has increased. We’ll go over the main procedures from design and programming to machining and finishing. Comprehending these methods will give you helpful information about using CNC machining to produce complex, high-quality components.
Design Considerations
Design considerations are crucial to streamlining the production process when employing CNC machining for complicated items. Manufacturers can guarantee effective manufacturing and achieve the required functioning of the finished components by carefully addressing various aspects during the design process. The following are some crucial design factors:
- Design for Manufacturability: It’s critical to design items with CNC machining in mind. Consider the CNC machine’s capabilities and restrictions, such as tool access, machine travel, and component orientation. To reduce complexity and make machining processes simpler, optimize the component geometry.
- Selection of Materials: The material is determined by the part’s functional needs, such as its mechanical qualities, chemical resistance, and environmental variables. Various materials could call for particular machining techniques and tooling concerns.
- Tolerances and Surface Finishes: Early in the design phase, decide what tolerances and surface finishes are necessary for the item. High accuracy may be achieved using CNC machining, although manufacturing time and cost may rise with tighter tolerances and better surface finishes.
- Part Consolidation: Wherever it is practical, consider combining many components into one part. This streamlines the production process while reducing assembly time and possible failure sites. Use CNC machining to produce complicated geometries that combine several elements into a single component.
- Design Simplicity: To maximize production efficiency, simplify the design wherever you can. Avoid adding complexity that isn’t essential since it may lengthen manufacturing times, increase tooling needs, and introduce mistakes. Consider the simplicity of machining processes, such as avoiding undercuts or complex geometries that could need specialized tools.
- Prototyping and Iteration: CNC machining allows rapid prototyping and iterative design improvements. Utilize this capacity by building prototypes to verify the design and make required changes before moving on with large-scale manufacturing.
Manufacturers may guarantee that the design is appropriate for CNC machining by considering certain design factors, leading to effective production, lower costs, and complicated components of excellent quality. Collaboration between designers and machinists is essential to maximize the design for manufacture and make the most of CNC machining technology.
Programming and Toolpath Generation
After completing the design process, the 3D model must be converted into CNC-compatible machine instructions. Toolpath generation and programming are terms used to describe this process. An outline of the main procedures is provided below:
CAM applications:
This program uses the 3D model to produce a set of instructions that direct the CNC cutter in precisely cutting the material.
Tools chosen:
Choose suitable cutting tools depending on the material and intricacy of the item. Think about cutting speed, stiffness, rigidity, and tool diameter.
Machining specifications:
The material, tooling, component shape, and desired surface polish all affect these factors.
Verification via simulation
To find any possible problems or collisions, simulate the toolpaths before running the software on the CNC machine. Verification assures the program’s correctness and assists in preventing expensive errors.
CNC Machining Process
It’s time to begin the CNC machining procedure now that the programming and toolpath development has been finished.
Workpiece Setting Up:
Clamps, vises, or fixtures are used to hold the raw material, generally in the shape of a block or sheet, onto the work table of the CNC machine. Make sure the material is level and correctly positioned.
Machine Configuration:
Equate the correct cutting tools in the machine’s tool holder. Calibrate the machine by establishing the work and tool offsets to ensure the cutting tool is positioned precisely.
WCS:
Work Coordinate System Establish the work coordinate system, which specifies the machine’s reference point concerning the component’s origin. By doing this, precise machining and repeatable measurements are guaranteed.
Machining Operations:
Execute the programmed toolpaths, which, depending on the complexity of the component, may combine cutting, drilling, milling, turning, and other operations. The CNC machine accurately moves the cutting tool along the predetermined route to form the material.
Monitoring and upkeep of the tool:
During the machining process, keep an eye on the cutting tools to ensure they operate at their best. To preserve quality and accuracy, examine tools often and replace any that are worn out or broken.
Finishing and Quality Control
The produced item may need extra finishing processes to attain the required surface quality and precision after the CNC machining process. Quality control techniques are crucial to guarantee that the finished product complies with the criteria. Think about the following actions:
Cleaning the surface and deburring
Utilize deburring equipment or techniques to eliminate any burrs or jagged edges. Apply surface treatments like polishing, coating, or sanding to improve aesthetics and prevent corrosion.
Dimensional analysis
To ensure that the part’s dimensions and tolerances meet the requirements, use precision measuring instruments like coordinate measuring machines (CMM), gauges, or calipers.
Quality Control:
Utilize methods for quality control, such as statistical process control (SPC), to keep an eye on and maintain a high level of consistency in the product throughout the production process. Analyze and collect data regularly to spot patterns and solve any possible problems.
Conclusion
For producing intricate pieces, CNC machining has fantastic possibilities. Manufacturers may create high-quality components by integrating compelling design considerations, programming strategies, and rigorous machining procedures. CNC machining is a flexible and dependable option for producing complicated parts because it can create complex shapes, deal with various materials, and maintain precise tolerances. CNC machining will play a more significant part in determining the future of manufacturing as technology develops.