Delrin or Acetal, polyoxymethylene (POM), is a famous CNC machining material. Various industries use it for its excellent mechanical qualities and dimensional stability. Optimizing outcomes and efficiency requires understanding POM CNC machining. In this book, we’ll examine POM CNC machining basics, methods, problems, and best practices.
POM Material Properties Understanding
A high-density thermoplastic made of repeated oxymethylene (-CH2O-) units, polyoxymethylene (POM) is also known as Delrin or Acetal. CNC machining applications benefit from POM’s mechanical strength, stiffness, and dimensional stability.
POM is appropriate for mechanical stress and frictional forces because of its high tensile strength, stiffness, impact resistance, low friction, and wear resistance. Heat stability, low thermal expansion, and temperature resistance assure dimensional correctness throughout machining and service.
Additionally, POM resists solvents, fuels, and chemicals, making it useful in many sectors. Due to its glass-like chips, POM machining needs careful tool selection, cutting settings, and coolant/lubrication methods to achieve the required surface qualities.
Setup for CNC Machining
To get the best results, POM CNC machining requires considerable preparation. Mechanical qualities, dimensional constraints, and chemical resistance must be considered while choosing a material grade.
Stock preparation requires POM sheets, rods, or blocks of the correct sizes for the component. Preparing stock maximizes material use and reduces machining waste.
The choice of cutting tools is crucial for accurate cuts and tool life. Since POM is abrasive, sharp carbide or HSS tools are utilized to machine it.
Secure the workpiece, attach cutting tools, and configure the CNC machine with toolpaths and machining settings. Correct machine setup provides precise machining.
Toolpaths for CNC machining need CAM programming. To optimize toolpaths, CAM software considers tool geometry, cutting pressures, and material removal rates.
Manufacturers may speed up POM CNC machining, reduce mistakes, and produce high-quality components by correctly preparing them.
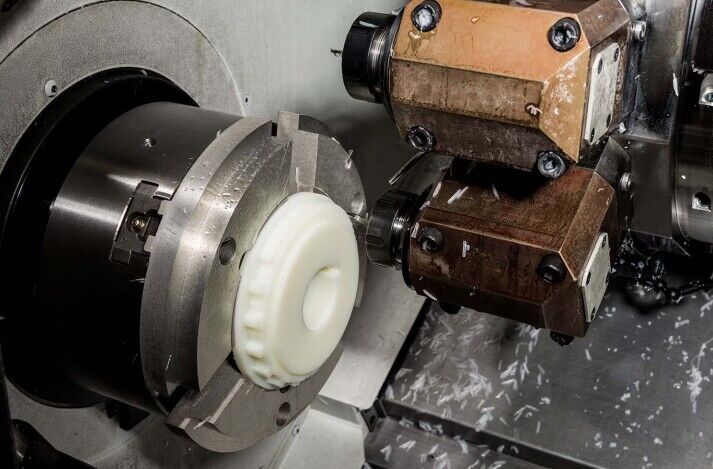
POM CNC Machining Tech
Precision POM component shaping includes milling, turning, drilling, thread machining, engraving, and surface finishing.
Milling removes material using rotary cutters. POM may be face milled, contour milled, and pocket milled to match specified forms and features.
A workpiece is rotated against a fixed cutting tool to make cylindrical components in turn. CNC lathes can turn POM shafts, pins, and other cylindrical pieces.
Creating holes in POM components requires drilling. For precise, burr-free holes, choose the right drill, cutting settings, and coolant/lubrication.
POM threads are cut via taps or thread mills. Correct thread pitch, depth, and diameter are essential for thread fit and functioning.
Precision engraving marks POM surfaces with ornamental or valuable markings. CNC engraving equipment with diamond or carbide cutters can do delicate work accurately.
Sanding, polishing, and chemical treatments may be used to obtain desired surface textures, gloss levels, and functional qualities on POM components.
Manufacturers may make POM components with exact geometries, tight tolerances, and high-quality surface finishes using CNC machining.
Best Practices for POM CNC machining
Efficient POM machining requires optimizing cutting settings, employing coolant and lubricant, maintaining tools, managing chips, fastening workpieces, and limiting heat impacts.
According to material grade, tool geometry, and machining operation, cutting speed, feed rate, and depth of cut should be chosen. The best cutting settings for an application may need experimentation and testing.
Coolant and lubrication reduce friction, heat, and chip accumulation in POM machining. Water-based coolants or plastic-specific lubricants are utilized to prolong tool life and finish.
Keeping cutting tools sharp, changing dull inserts, testing for wear, and cleaning tool holders and collets are crucial for consistent machining performance and tool life.
Preventing chip recutting, tool deflection, and surface flaws requires chip control in POM machining. Use chip breakers, peck drilling, or through-tool coolant to preserve process stability and component quality.
Preventing component movement or vibration during machining requires clamping, fixtures, or vacuum systems. The proper support and stiffness reduce dimensional mistakes and guarantee precise machining.
Dimensional accuracy and surface smoothness depend on minimizing thermal effects such as material expansion or warping owing to heat accumulation during machining. Heat dissipation, cutting force control, and tool shape optimization may reduce thermal concerns.
These best practices enhance POM CNC machining operations, boost productivity, and ensure high-quality outcomes.
Solutions to Common Issues
In POM CNC machining, chip formation, tool wear, built-up edge, surface polish concerns, dimensional imperfections, and environmental variables are prevalent problems with remedies.
In improperly handled POM machining, chip entanglement, poor surface quality, and tool wear may result. Proper cutting settings, chip breakers, and coolant/lubrication may increase chip evacuation and avoid chip problems.
The abrasiveness and intense cutting pressures of POM cause tool wear and breakage. Quality cutting tools with suitable coatings, optimum cutting settings, and frequent tool wear monitoring may extend tool life and minimize machining costs.
When material clings to the tool’s cutting edge, built-up edge (BUE) development causes poor surface quality and dimensional errors. Managing cutting settings, tool shape and chip evacuation may reduce BUE development and increase machining performance.
Roughness, chatter marks, and surface tear-out may result from poor tool selection, cutting parameters, or coolant/lubrication in POM machining. The right tool geometries, machining conditions, and fine-grit cutting or polishing tools may assist in achieving desirable surface qualities.
In POM machining, tool deflection, workpiece movement, and temperature impacts may cause dimensional errors. Keep machining processes accurate and consistent by clamping workpieces, reducing cutting forces, and managing heat.
Material characteristics and POM CNC machining performance may be affected by temperature and humidity. Stable machining conditions, coolant/lubricant temperatures, and environmental monitoring may reduce the effect of external influences on machining operations.
Manufacturing companies may overcome POM CNC machining hurdles and produce high-quality outputs by knowing and addressing these issues.
Remarks After Machining
To assure product quality, post-machining includes cleaning, deburring, inspection, quality control, surface treatment, and packing.
To remove coolant, lubricant, and swarf and maintain surface integrity, POM components must be cleaned after machining. Mild detergents, ultrasonic cleaning, and solvent rinses may clean POM components.
Remove sharp edges, burrs, or extra material from machined POM components to enhance safety, functionality, and aesthetics. Manual deburring, tumbling, abrasive blasting, or vibratory finishing depends on component shape and surface requirements.
Inspection of machined POM components is essential for dimensional correctness, surface polish, and design conformity. Measurement instruments, including callipers, micrometres, CMMs, and optical comparators, may conduct dimensional inspections and quality checks.
Quality control checks that machined POM components fulfil performance and quality requirements. Product quality and customer satisfaction depend on process controls, audits, and responsiveness to non-conformities.
To improve look, durability, and usefulness, machined POM components might be polished, buffed, or coated. Application-specific surface treatments may address corrosion, wear, or aesthetics.
Packaging machined POM components securely prevents damage during handling, shipping, and storage. Parts arrive securely and intact with proper packing, padding, and labelling.
Manufacturers may ensure quality, reliability, and customer satisfaction of machined POM components by being careful with post-machining.
CNC POM Machining Uses
POM is versatile enough for automotive, aerospace, electronics, medical, and consumer goods applications.
The car sector uses POM to make gears, bushings, bearings, fuel system components, and interior trim. Its strength, wear resistance, and dimensional stability make it perfect for demanding automotive applications.
Aircraft interior fittings, structural components, and fasteners are made from POM in aerospace and aviation. Advanced mechanical qualities, chemical resistance, and reduced moisture absorption make it suitable for aerospace applications.
The electronics and electrical sector uses POM to make connections, insulators, switches, and housings because of its electrical insulation, dimensional stability, and moisture and chemical resistance. Ideal for electrical applications because of its excellent dielectric strength and thermal stability.
Surgical tools, implants, medication delivery devices, and laboratory equipment are made from POM. Its biocompatibility, sterilizability, and chemical resistance make it excellent for medical usage.
Zippers, buckles, handles, knife handles, and gears in consumer items and sports equipment are made from POM. The smooth surface, minimal friction, and durability make it perfect for consumer items and enjoyment.
Utilizing the material’s outstanding features and performance, POM CNC machining allows manufacturers to create a broad selection of precise components for various applications.
New ideas and trends
CNC innovation, sustainable machining, digitization, and material development are driving POM CNC machining trends.
POM machining businesses may increase precision, efficiency, and production using CNC technology, including greater machine accuracy, spindle speeds, and control systems.
Decreased material waste, optimized energy usage, and recycled coolant/lubricant fluids are becoming more significant in POM CNC machining to decrease environmental impact and improve resource efficiency.
Intelligent manufacturing technologies like predictive maintenance, real-time monitoring, and data-driven decision-making may optimize machining operations and increase production performance with digitalization and Industry 4.0 integration.
Formulation adjustments, additives, and composite materials improve POM attributes, including wear resistance, frictional properties, and flame retardancy, to fulfil industrial and application needs.
By adopting these future trends and advancements, firms may remain ahead, seize new possibilities, and enhance POM CNC machining processes and capabilities.
Conclusion
POM CNC machining demands material knowledge, careful preparation, proper technique, best practices, and ongoing progress. With the appropriate knowledge and skills, POM can provide durable, accurate, and dependable components to many industries.
This tutorial helps engineers, machinists, and manufacturers use POM in CNC machining. Manufacturers may fulfil current production standards and drive industry innovation by using the material’s excellent qualities and performance to make high-quality components quickly and effectively.