Time-Saving
The industry of rapid prototyping has completely changed how businesses create and refine their product ideas. The term “rapid” refers to how a product is developed. This article examines a few time-saving techniques producers in the quickly developing rapid prototyping industry should know.
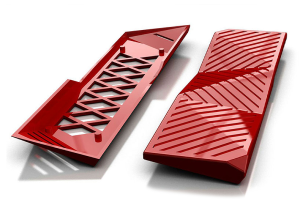
3D Printing
The ability of manufacturers to swiftly and precisely translate digital ideas into actual items has transformed how they create prototypes.
Traditional manufacturing procedures like tooling and machining, which may be time-consuming and expensive, are replaced by 3D printing. Instead, it makes it possible for manufacturers to create working prototypes from CAD models. Layers of material are deposited one at a time as the prototype is constructed from scratch.
The capacity to quickly iterate through a design is one of the main benefits of using a 3D printer. Modifications to the design may be quickly applied without the requirement for extra machinery or a significant amount of labor. Due to their ability to adapt swiftly to customer input and testing, manufacturers may explore many design iterations.
Additionally, 3D printing provides a vast selection of materials, including different polymers, metals, ceramics, and composites. This adaptability enables producers to produce prototypes that closely match the finished product in terms of aesthetics and mechanical characteristics. Manufacturers may speed up the product development process by conducting more accurate testing and assessment by employing materials with attributes that are comparable to those of the desired final product.
The capacity of 3D printing to combine several pieces into a single produced component is another time-saving feature. The assembly of several separate pieces is a common need of traditional manufacturing techniques, which may be labor-intensive and complicated. Complex geometries may be produced using 3D printing in a single piece, which cuts down on assembly time and possible weak areas.
Additionally, 3D printing speeds up the process of rapid prototyping by cutting down on setup and tooling lead times. Before production, molds die, or fixtures must be created for traditional manufacturing procedures. Comparatively, 3D printing does away with the necessity for tooling, enabling quicker turnaround times and condensed development cycles.
In conclusion, 3D printing has a lot of time-saving benefits for rapid prototyping. The use of various materials, including wood, metal, and plastic, and the capacity to rapidly and easily switch between them are all hallmarks of a successful business. Manufacturers may hasten product development, save expenses, and speed up the release of novel items to market by using the advantages of 3D printing.
Rapid Injection Molding
Producers may also use rapid injection molding to save time in the field of rapid prototyping. The advantages of conventional injection molding are combined with the speed and adaptability necessary for rapid prototyping in this method.
Rapid injection molding uses soft tooling of materials like aluminum or 3D-printed polymers instead of traditional metal molds. Mold creation takes far less time and money when soft tooling is used. In contrast to the weeks or months required for traditional tooling, these molds may be made in a matter of days.
Manufacturers can rapidly iterate and improve their ideas because of the speedy fabrication of molds. Rapid design changes may be made, enabling more flexible and responsive prototyping. This adaptability is especially useful in the early phases of product development when design modifications are frequent.
It’s important to note that most of these companies products are made in the United States. Before committing to full-scale manufacturing, this capacity allows firms to assess market demand and obtain insightful feedback. Manufacturers may assess the product’s usability, appeal, and user experience, spot any possible problems, and make the required adjustments by only making small units. This iterative process lowers the hazards of producing a product in significant numbers that may later need costly adjustments.
Compared to conventional injection molding for low-volume manufacturing, rapid injection molding also provides cost benefits. Manufacturers may create a small batch of items using soft tooling without paying the significant upfront expenses of making metal molds. For producers that need to test their ideas while keeping production costs under control swiftly, rapid injection molding is a desirable alternative due to its cost advantage.
Rapid injection molding may also be used with various materials, such as different plastics and elastomers, allowing producers to choose the material that would work best for their prototype. This ensures that the prototype closely resembles the desired final product regarding functionality and performance.
In summary, rapid injection molding is a time-saving strategy that gives producers the benefits of conventional injection molding while drastically lowering lead times and costs. Soft tooling enables manufacturers to carry out low-volume production runs for testing and feedback, rapidly iterate and improve their ideas, and choose appropriate materials for their prototypes. Rapid injection molding enables producers to quicken the prototyping process, make wise judgments, and get closer to the successful commercialization of their products.
CNC Machining
The term “computer-aided design” (CADD) refers to the process of creating a computer program. Using computer-aided design (CAD) data, this precision manufacturing method molds raw materials into workable prototypes.
Because of its high precision, CNC machining is an excellent option for producing prototypes with complex geometries and exact tolerances. Prototypes that closely mirror the final product in terms of size and surface polish are produced because of the ability to regulate the cutting tools and machine movement. The aerospace, automotive, and medical device sectors, which need complicated components, particularly benefit from this precision.
The ease with which prototypes may be made is one of the main benefits of CNC machining. The CNC machine can swiftly convert the produced CAD model into an actual prototype by removing extra material. The following is a list of all the companies that provide this service.
Additionally, a variety of materials, such as metals, polymers, and composites, are supported by CNC machining. Manufacturers may choose the best material for their prototype, ensuring that it closely resembles the desired finished product in terms of functionality and performance. During the early phases of product development, producers may test and assess the prototype’s mechanical qualities, including strength and durability, thanks to the material’s adaptability.
Additionally flexible in terms of design revisions is CNC machining. Manufacturers may update the CAD model and run it through the CNC machine to make an updated prototype. Due to its agility, the final product may be quickly modified and improved in response to testing and user input, guaranteeing that the necessary parameters are met.
Additionally, CNC machining works well for low-volume manufacturing runs. The same CNC machine may create a small batch of components once the prototype has been approved and is prepared for limited-scale manufacture. With the aid of this capacity, producers may transition products from the prototyping stage to full-scale manufacturing while preserving accuracy and quality.
In conclusion, CNC machining is a time-saving strategy that combines high precision, material diversity, and rapid production capabilities. Manufacturers can swiftly produce prototypes with intricate geometries and exact tolerances using CNC machines, choose the best materials, iterate designs effectively, and go seamlessly from prototyping to low-volume manufacturing. The term “soap” refers to converting raw materials into usable ones.
Conclusion
Time is crucial for producers in the rapid prototyping industry who want to bring new items to market quickly. Manufacturers may dramatically shorten development cycles and simplify prototyping by adopting time-saving techniques like 3D printing, rapid injection molding, and CNC machining. These strategies enable manufacturers to quickly develop ideas, run functional tests, and obtain insightful feedback before starting full-scale production. Manufacturers should keep up with the most recent innovations as rapid prototyping technologies grow to fully use these time-saving strategies and acquire a competitive edge in their particular markets.