Aluminum is a common metal option for product designers due to its excellent physical characteristics and good workability. Even if you have developed aluminum components or parts, you do not want to continue manufacturing them without first creating a prototype. In this blog, we will tell you the best ways to create aluminum prototypes in less time and budget.
Aluminum is the most often utilized material in the manufacture of prototypes. Durable machinery and structural components are required in various sectors, including aerospace, medical, and automotive.
Manufacturers produce aluminum prototypes in a number of methods, depending on the need. They may employ 3D printing, aluminum prototype machining, or aluminum casting services, depending on the component, the quantity, and the form of the part.
Each of these techniques has several distinct benefits and drawbacks. Making the incorrect decision may result in increased tooling and production expenses and non-functional and useless components.
This blog discusses the many aluminum prototyping techniques available to assist you in determining which approach is appropriate for your prototype project.
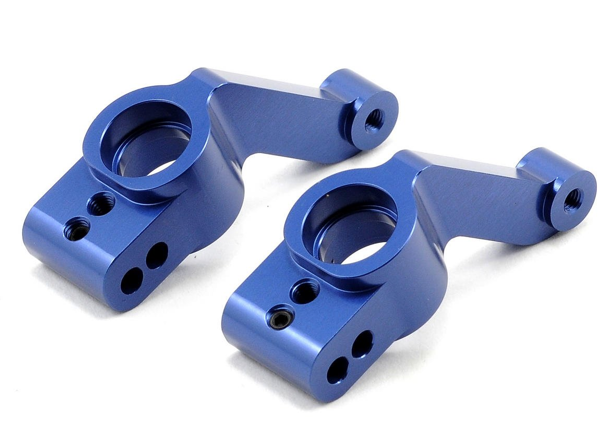
Aluminum Prototype Manufacturing: What Is It?
Aluminum prototyping is a fast manufacturing method that begins with aluminum blocks. This method utilizes a variety of technologies and equipment to create the greatest possible design.
Manufacturers and designers strive to get their finished goods to market as quickly as feasible, and it is done to save both time and money. As a result, a sample was created that was very similar to the actual product.
Aluminum goods are in high demand and find use in a variety of sectors. Aluminum prototype makers create prototypes before mass manufacturing high-end goods and these prototypes aid in the design’s refinement.
Main Three Methods for Making Aluminum Prototypes
Method #1: CNC Manufacturing Technology
Processes on a case-by-case basis based on design files.
The case-by-case Aluminum prototype machining technique utilizes computer input to accurately control the cutting tool, removing unwanted portions of the aluminum workpiece while leaving the necessary portions. Additionally, since it is a subtractive manufacturing process, it will result in material waste. However, what distinguishes CNC machining from other processes, and when should it be used?
CNC Aluminum prototype machining produces high-quality parts with a great surface polish and repeatability. Also suitable with a wide variety of aluminum alloys, it is an excellent choice.
CNC machining is especially well-suited for prototyping and testing. You may build complicated prototypes that are tough to manage with conventional machining techniques with 4-axis and 5-axis CNC milling machines.
Method #2: 3D Printing
Another common method for creating aluminum prototypes is 3D Printing, which utilizes additive manufacturing methods to minimize waste. As with Aluminum CNC prototype machining, 3D printing utilizes 3D CAD models to produce precise aluminum prototypes.
Its minimal feature size is between 0.25 and 0.8 mm, which enables the fabrication of complicated geometries with complex interior cross-sections. 3D printed aluminum prototypes, on the other hand, are not inexpensive and often need additional surface treatment.
Aluminum prototypes created through 3D Printing are often more costly than those created by Aluminum prototype machining. As a result, 3D Printing is more suited to producing tiny components, particularly test versions and production prototypes.
Method #3: Investment Casting
Metal components are manufactured here by pouring molten aluminum into wax molds. Making molds is a costly procedure due to the specialized equipment required. Investment casting produces parts with high surface quality, adheres to tight dimensional tolerances, and is compatible with a wide range of aluminum alloys.
Additionally, investment casting produces less material waste than Aluminum CNC prototyping. Although this technique has certain advantages, it has some disadvantages as well.
Aluminum Prototypes Advantages
We may make prototypes from various materials depending on the component, purpose, and required strength. Aluminum, on the other hand, is chosen for aesthetic and practical reasons. Consider the following as a few benefits of utilizing aluminum prototypes in your next project:
Increased heat resistance
The heat resistance property is very useful while creating prototypes. The aluminum prototype is resistant to high heat. As a result, it will be less susceptible to deterioration throughout the manufacturing process unlike other materials like plastic.
Superior Aesthetics
Metal prototypes appear better regardless of whether they are created using 3D printing or CNC milling technologies. Additionally, they are more visually appealing than plastic components, even when used as non-functional prototypes.
Cost-effectiveness
In comparison to plastic components, aluminum prototypes and metal components are much less expensive. Metal’s physical characteristics help decrease the frequency with which components need to be replaced, resulting in long-term cost savings.
Test accuracy
CNC machining and other techniques produce very accurate prototypes. Additionally, aluminum alloys are very durable and can be used to create components for market testing.
More suited to scaling
After the engineer completes the aluminum prototype, the client may proceed with manufacturing. It is simpler to convert a metal prototype into a completed product than a plastic prototype into a finished one. However, if the prototype is constructed of plastic, mass manufacturing can not convert it to metal.
Super Strength
They are extensively utilized in the majority of sectors due to their superior features. Aluminum components, for example, are extensively utilized in the aircraft sector. As a result of this advantage, clients may be certain to get high-quality components and prototypes.
Summary
We hope the above information will help you create an aluminum prototype in the best possible way. From design to surface treatment technologies, China’s one-stop-shop offers best-in-class aluminum prototype services. The generated prototype is subjected to CNC milling, turning, polishing, and anodizing to produce a flawless prototype. Industrial customers are not required to transport their prototypes to another location while using these services.
We are a licensed precision machining business with years of expertise in CNC Aluminum prototype machining services such as CNC milling, turning, grinding, EDM, and wire EDM. Our team has a decade-long experience in this field and is always ready to assist you.