CNC precision machining has changed manufacturing by allowing the creation of delicate and accurate components across sectors. This thorough book will explain the concepts, processes, and applications of CNC precision machining and the importance of machining parts in modern manufacturing.
Principles of CNC Precision Machining
CNC precision machining uses fundamental concepts for accuracy, efficiency, and versatility. CNC machining uses computer numerical code to control cutting tools. The main ideas are:
1.Computer Programming: CNC precision machining starts with a comprehensive program. This application converts design parameters into CNC machine commands for tool movements, speeds, and feeds.
2.Automation: CNC machining offers automation as a critical benefit. After programming, the CNC machine runs automatically, reducing manual supervision. Automation improves manufacturing efficiency and consistency.
3.Precision Control: CNC machines provide accurate movement of cutting tools and workpieces. Complex positioning systems ensure that machining follows design standards.
4.Real-time Adjustments: CNC machining enables real-time adjustments during manufacture. For optimal machining results, operators can adjust cutting settings or toolpaths.
CNC precision machining’s high-precision capabilities and flexibility in producing complex and exact components across sectors depend on operators and manufacturers understanding these fundamentals.
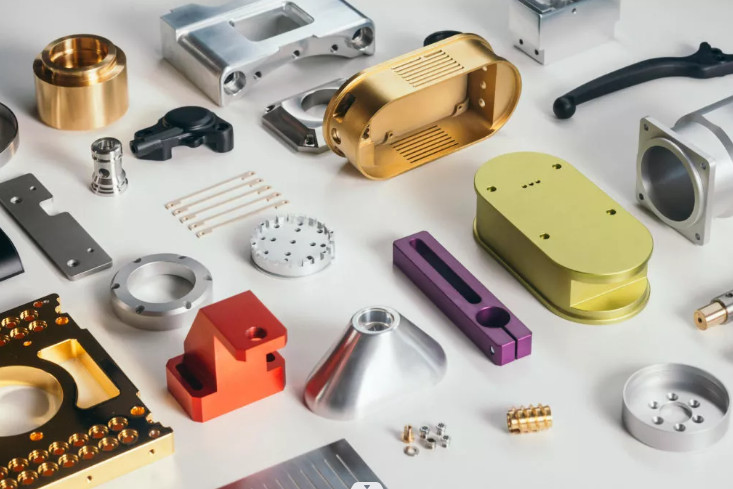
CNC Precision Machining Techniques
CNC precision machining shapes materials into complex parts using numerous methods. These methods improve accuracy and efficiency with improved computer control. Essential CNC precision machining methods:
Milling:
●Multi-axis milling machines enable simultaneous movement along multiple axes, allowing for the creation of intricate three-dimensional parts.
Turning:
●This technique is commonly used for producing shafts, bushings, and other cylindrical components with high precision.
Electrical Discharge Machining (EDM):
●CNC EDM employs electrical discharges to erode material from the workpiece, allowing for machining intricate shapes in hard materials.
Laser Cutting:
●This technique is suitable for various materials, including metals and plastics, and is commonly used for creating detailed patterns.
Grinding:
●It is particularly effective in achieving tight tolerances and fine surface finishes for components.
Drilling:
●CNC drilling involves creating holes in a workpiece with precision and accuracy.
●Various CNC drilling machines are used, ranging from simple single-spindle drills to multi-axis machines for complex hole patterns.
CNC precision machining methods depend on the component being made. CNC machining is essential to modern manufacturing across many industries because it allows producers to program and control these procedures precisely to build products with tight tolerances and sophisticated geometries.
Materials Used in CNC Precision Machining
CNC precision machining can use various materials chosen for their qualities and uses. CNC precision machining uses materials like:
Metals:
●Aluminium, stainless steel, titanium, and various alloys are frequently machined due to their strength, durability, and excellent machinability.
Plastics:
●CNC machining is ideal for engineering ABS, acrylic, and PEEK polymers. These versatile, precise machining materials are employed in electronics, healthcare, and consumer goods.
Composites:
●Composite materials, such as carbon fiber-reinforced plastics, are used in aerospace and automotive applications. CNC precision machining produces strong-to-weight components.
Ceramics:
●High-performance ceramics, including alumina and zirconia, are chosen for their exceptional hardness, wear resistance, and thermal stability. CNC machining enables the production of intricate ceramic components for specialized applications.
CNC precision machining’s versatility in various materials allows producers to create accurate and sophisticated components adapted to each application.
Applications of CNC Precision Machined Parts
CNC precision machined parts find extensive applications across diverse industries, pivotal in producing intricate and accurate components. Key applications include:
Aerospace Industry:
●CNC precision machining is critical in aerospace for manufacturing components like aircraft engine parts, structural elements, and intricate components, which are essential for lightweight yet durable materials.
Automotive Industry:
●In automotive manufacturing, CNC precision machined parts produce engine components, transmission parts, and intricate components that require high precision and reliability.
Electronics:
●CNC precision machined parts are employed in the electronics industry for manufacturing components such as connectors, housings, and heat sinks. The precision ensures optimal functionality in electronic devices.
Oil and Gas:
●CNC machining is used in the oil and gas industry to produce components for exploration, drilling, and extraction equipment. The precision and durability of machined parts are vital in harsh operating conditions.
Consumer Goods:
●CNC precision machined parts produce consumer goods, including high-end watches, cameras, and other premium products where precision and aesthetic appeal are essential.
Advantages of CNC Precision Machining
CNC precision machining has many benefits that make it popular across industries. CNC machining produces high-quality components efficiently, accurately, and versatilely.
Key benefits:
1.High Accuracy: CNC machines produce items with impeccable tolerances and requirements.
2.Enhanced Efficiency: CNC machining automates operations, minimizes manual labour, and optimizes toolpaths for effective material removal.
3.Greater Flexibility: CNC machines handle diverse materials and geometries, making them useful for various applications.
4.Improved Reproducibility: CNC precision machining guarantees consistent repetition of identical parts in large-scale production.
Challenges and Considerations in CNC Precision Machining
CNC precision machining has many benefits, but producers must overcome its drawbacks.
1.Programming Complexity: CNC machines demand trained operators for precise and efficient toolpath creation.
2.Regular maintenance is crucial for maintaining CNC machines and ensuring constant performance.
3.Material Selection: Consider machinability, strength, and thermal conductivity while selecting CNC machining materials.
Future Trends in CNC Precision Machining
CNC precision machining is evolving rapidly due to technology and industrial demands. Multiple trends are expected to shape CNC precision machining in the future:
1.AI Integration: AI can improve CNC machining processes by optimizing toolpaths, forecasting maintenance needs, and increasing efficiency.
2.The use of CNC machines with 5-axis and multi-axis capabilities will increase, enabling the manufacturing of more complicated and sophisticated parts.
3.Additive Manufacturing Integration: CNC machining and additive manufacturing technologies provide hybrid products with improved functionality and reduced waste.
4.Implementing IoT technology in smart factories will enable real-time monitoring and management of CNC machining processes, increasing efficiency and quality.
Conclusion
As technology advances, AI, sophisticated machining, and smart factories will improve CNC precision machining. Manufacturers seeking to produce high-quality, accurate components for today’s numerous sectors must understand CNC precision machining concepts, processes, applications, and future trends. If you would like to know more about advanced industry technologies , please contact our team .