CNC MACHINING
CNC (Computer Numerical Control) machining has revolutionized the manufacturing industry, offering precision and repeatability in producing intricate parts and components. Tolerance standards are crucial in CNC machining, defining the acceptable deviation from a desired dimension or specification. Understanding these tolerance standards is essential for manufacturers and engineers to ensure the quality and functionality of machined parts. This comprehensive guide will delve into the critical tolerance standards you need to know for CNC machining.
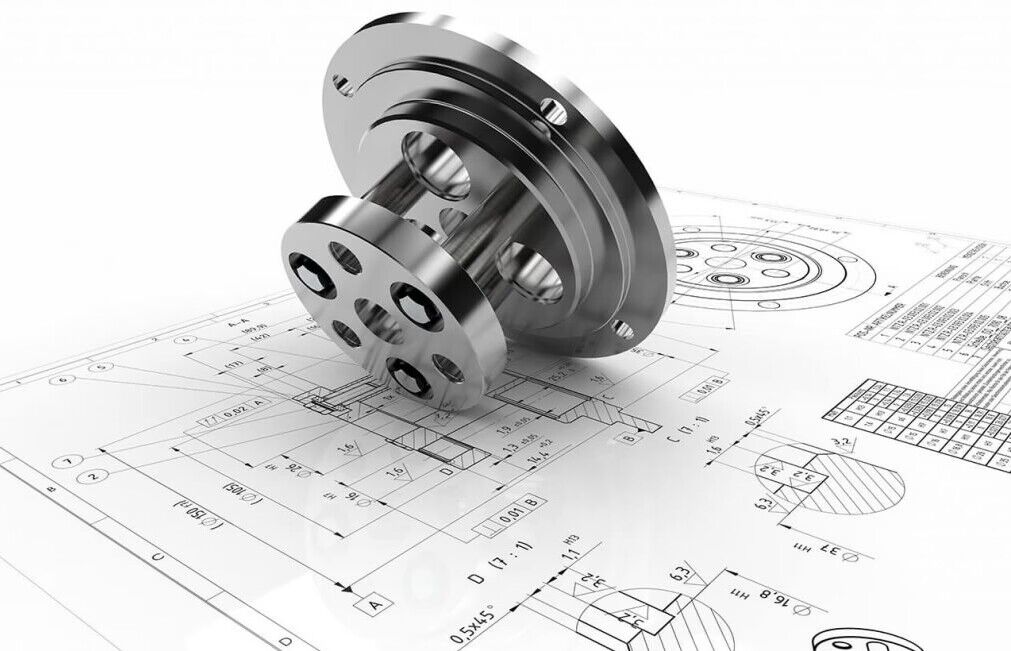
What Are Tolerance Standards in CNC Machining?
Tolerance standards in CNC machining refer to the allowable variation in dimensions and other critical specifications of machined parts. Tolerance standards are typically expressed in numerical values, such as ±0.001 inches or ±0.025 millimeters, which indicate the maximum allowable deviation from the nominal dimension.
ISO Tolerance Standards
The International Organization for Standardization (ISO) has established a widely accepted set of tolerance standards for CNC machining. ISO 2768 is divided into several parts, each specifying different tolerance classes, ranging from fine to coarse.
Here are some critical points regarding ISO tolerance standards:
- ISO 2768-1: This part of the standard covers linear dimensions and is divided into four tolerance classes: IT01, IT0, IT1, and IT2. IT01 is the tightest tolerance class, while IT2 is the loosest.
- ISO 2768-2: This standard part focuses on angular dimensions and provides tolerance classes IT5, IT6, IT7, and IT8.
- ISO 2768-3: Part 3 deals with symmetry tolerances and includes classes IS01, IS0, IS1, and IS2.
- ISO 2768-4: Part 4 addresses the flatness and straightness of surfaces and includes tolerance classes IF01, IF0, IF1, and IF2.
- ISO 2768-5: This part defines the tolerance classes for perpendicularity, which are IP01, IP0, IP1, and IP2.
ISO tolerance standards provide a comprehensive framework for specifying tolerances in CNC machining, ensuring that parts meet the required quality standards while allowing for flexibility in the manufacturing process.
ANSI Y14.5 Geometric Dimensioning and Tolerancing (GD&T)
GD&T is a more advanced and comprehensive system for specifying tolerances in CNC machining, particularly for complex parts with geometric features.
Critical aspects of ANSI Y14.5 GD&T include:
- Datums: GD&T uses datums as reference points to establish the coordinate system for measuring dimensions and tolerances. Datums help ensure consistent and repeatable measurements.
- Feature Control Frames: Feature control frames communicate specific geometric tolerances for features like holes, slots, and surfaces. These frames include symbols and modifiers that convey the desired tolerance requirements.
- Position Tolerance: GD&T includes position tolerance, which defines the acceptable deviation of a feature’s position from its specified location. This tolerance is beneficial for parts with multiple interacting features.
- Form Tolerances: GD&T specifies form tolerances for features such as flatness, straightness, circularity, and cylindricity. These tolerances ensure that the form of a feature meets design requirements.
- Profile Tolerance: Profile tolerance controls the shape and location of a feature’s boundary. It ensures the entire surface or feature conforms to the specified profile within the defined tolerance zone.
ANSI Y14.5 GD&T is widely used in industries where precise geometric control is critical, such as aerospace, automotive, and medical device manufacturing. It allows for the unambiguous communication of design intent and ensures that parts function as intended.
ASME Y14.8 Castings and Forgings Tolerances
This standard addresses the unique challenges of machining cast and forged parts, which often have irregular shapes and surface conditions.
Critical features of ASME Y14.8 include:
- Casting and Forging Symbols: ASME Y14.8 introduces symbols and conventions specific to castings and forgings, making it easier to specify tolerances for these types of parts.
- Surface Finish Requirements: The standard provides guidelines for surface finish requirements, as the surface condition of castings and forgings can significantly impact machining processes.
- General Tolerances: ASME Y14.8 includes general tolerances for dimensions, which vary based on the part size and the machining operation type.
- Minimum Material Requirements: The standard defines minimum material conditions to ensure enough material is present for machining and that critical features are maintained.
ASME Y14.8 is essential for manufacturers and engineers working with cast and forged components, helping them achieve the necessary precision and quality in CNC machining processes.
MIL-STD-1913 for Firearms and Accessories
MIL-STD-1913, the Picatinny rail standard, is relevant to the firearms and accessories industry. This standard defines the dimensions and tolerances for the Picatinny rail, a system used for attaching accessories such as scopes, sights, and laser aiming modules to firearms.
Critical aspects of MIL-STD-1913 include:
- Rail Profile: The standard specifies the Picatinny rail profile, including the slots’ dimensions and spacing. These dimensions are crucial for ensuring compatibility between different accessories and firearms.
- Tolerance Requirements: MIL-STD-1913 provides tolerance requirements for critical dimensions of the Picatinny rail, ensuring that accessories can be securely mounted and aligned on firearms.
- Material and Coating Specifications: The standard also addresses material requirements and coating specifications to enhance durability and corrosion resistance.
MIL-STD-1913 is vital for the firearms industry, as it allows manufacturers to produce accessories compatible with a wide range of firearms while maintaining tight tolerances for reliable performance.
Application-Specific Tolerance Standards
In addition to the abovementioned standards, various industries and applications may have unique tolerance requirements based on their specific needs. For example:
- Aerospace: The aerospace industry often has stringent tolerance standards, especially for critical components like jet engine parts and aircraft structures.
- Electronics: The electronics industry relies on precise tolerances to ensure the proper functioning of components like printed circuit boards (PCBs) and semiconductor devices.
Conclusion
These are the CNC tolerance standards you need to know for CNC machining. Tolerance standards are fundamental to CNC machining, ensuring that machined parts meet the desired quality and functionality requirements. ISO tolerance standards, ANSI Y14.5 GD&T, ASME Y14.8, and industry-specific standards like MIL-STD-1913 provide the necessary guidelines for specifying tolerances in various applications.
Understanding and correctly applying these tolerance standards is crucial for manufacturers, engineers, and designers to achieve precision, reliability, and consistency in CNC machining processes. By adhering to these standards, industries can produce high-quality components that meet strict performance and safety criteria.