CNC Machine Introduction
CNC (Computer Numerical Control) machining is essential to contemporary manufacturing, providing unmatched accuracy, efficiency, and adaptability for complex items. CNC machining uses computerized controls to automate and precisely regulate cutting tools, unlike hand machining. This technical invention has transformed the aerospace, automotive, medical, and electronics sectors by improving design complexity, quality assurance, and manufacturing throughput. Manufacturers can accurately and repeatably turn raw materials into final components using CAD software and CNC programming. This thorough introduction will examine CNC machining’s underlying concepts, techniques, and applications, examining its transformational influence on contemporary production and its role in determining the industry’s future.
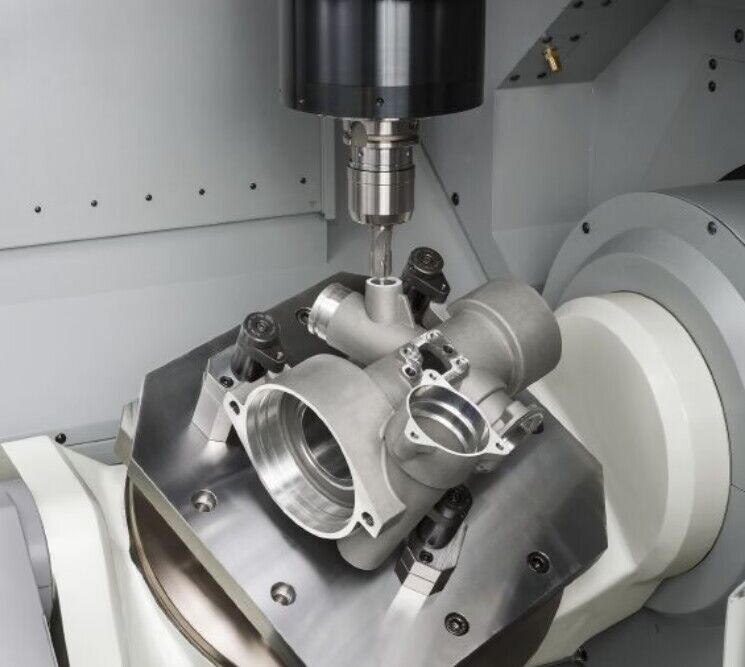
CNC Machining Basics
CNC (Computer Numerical Control) machining uses precision machines and digital controls to make complex items from raw materials. CNC machining automates machining using programmed instructions instead of trained workers controlling cutting instruments. CAD software determines the CNC machine’s tool trajectories, cutting speeds, and feed rates.
CNC machining requires a machine tool, a control unit, a workpiece holding mechanism, and cutting instruments. Machine tools like lathes and milling machines execute machining while the control unit interprets digital instructions and controls their motions. Workpiece-holding devices hold raw material during machining, whereas drills and end mills remove material.
CNC machining improves accuracy, repeatability, and efficiency over hand machining. It is used to make complicated parts with strict tolerances and accurate geometries in the aerospace, automotive, medical, and electronics sectors.
CNC Principle
CNC machining transforms raw materials into final components in a well-coordinated procedure. In CAD software, engineers carefully design the component’s size and requirements. Programmers then generate CNC code from these designs to control tool trajectories, cutting settings, and other machining parameters. After priming the CNC machine and attaching the workpiece, the CNC code’s careful instructions direct machining. After the CNC machining cycle ends, the completed component is carefully inspected for quality.
CNC Machine Operations
CNC machine operations achieve precision and efficiency by transforming raw materials into completed components. This technique uses computerized controls to perform difficult machining jobs accurately and repeatably.
CNC machining uses rotary cutting tools to mill complicated forms and features from a workpiece. For gears, brackets, and housings with complex geometries, this method is excellent.
CNC machining also includes turning the workpiece as a cutting tool to remove material to make cylindrical forms like shafts, rods, and bushings. Turning using CNC lathes produces exact cylindrical components.
Tools called drills produce holes in the workpiece during drilling. CNC drills can accurately drill holes of varied diameters and depths.
Abrasive wheels grind workpieces to smooth surfaces and precise tolerances. This method is utilized for the precision machining of rigid materials and components with exquisite finishes.
CNC machining allows manufacturers to make complex components with tight tolerances and high surface finishes for numerous industries.
CNC milling materials
CNC machining enables ordinary metals, sophisticated composites, and polymers. Due to their strength and adaptability, aluminum, steel, brass, and titanium are machined. Lightweight, corrosion-resistant ABS, acrylic, and nylon are often used. CNC machining also handles ceramics and unusual metals, expanding its industry applications. Machined component performance and functionality may be optimized by carefully choosing materials for particular applications.
CNC Machining Benefits
CNC machining changed manufacturing, offering several benefits that previous machining processes couldn’t match. CNC machines are best for accuracy since they consistently achieve tight tolerances and complicated geometries. This accuracy improves machined component quality and simplifies complicated designs and requirements. Automation and digital control technologies make CNC machining efficient. CNC machining decreases lead times and maximizes resource utilization by automating labor-intensive jobs and optimizing production processes.
Additionally, CNC machining can handle a wide range of materials and machining techniques for various purposes. The versatility and scalability of CNC machining systems provide manufacturers exceptional flexibility in meeting changing industrial needs. CNC machining empowers producers to push precise engineering and innovate, ushering in a new age of industrial excellence.
CNC Machine Uses
CNC machining underpins many applications across a wide range of sectors in almost every aspect of contemporary production. In aerospace, CNC machining is used to make engine parts, airframe structures, and interior fittings. For aerospace conditions, these components need accuracy and repeatability, which CNC machining provides. Automotive manufacturers use CNC machining to make engines, gearboxes, chassis, and interior trim parts. CNC machining accuracy and efficiency meet automotive applications’ strict performance and tolerance criteria. CNC machining is crucial to medical implants, surgical equipment, prostheses, and diagnostic technology. CNC machining methods provide biocompatibility, accuracy, and cleanliness for these components. Electronic enclosures, heat sinks, connections, and other essential elements are made using CNC machining. The accuracy and dependability of CNC machining are necessary for the smooth integration and operation of electrical systems in many applications. CNC machining drives innovation and excellence throughout sectors, as seen by these different uses.
CNC Machining Futures
CNC machining is interwoven with technological progress, which is reshaping contemporary production. CNC machining can now make complicated, customized components using additive manufacturing methods like 3D printing. By seamlessly merging additive and subtractive technologies, manufacturers may unleash unprecedented design flexibility and usefulness. Through process optimization, predictive maintenance, and adaptive control techniques, AI and machine learning will transform CNC machining. Artificial intelligence systems may find trends, adjust settings, and improve machining processes using massive data sets. Another frontier in CNC machining is automation and robotics, with robotic systems becoming more important in production operations. Robo-assisted material handling, component loading, tool change, and quality inspection speed up production and improve operating efficiency. These developments usher in a new age of production with unparalleled flexibility, efficiency, and creativity, placing CNC machining at the technical forefront.
Conclusion
CNC machining represents technology and human intellect, pursuing accuracy, efficiency, and innovation in production. CNC machines revolutionize contemporary production by seamlessly merging computerized control systems with superior machining processes. Precision and adaptability make CNC machining essential in almost every sector, from aerospace and automotive to medical and electronics. CNC machining will drive innovation, efficiency, and quality across industries as technology evolves. By using additive manufacturing, AI, and automation, firms may increase design flexibility, productivity, and sustainability. CNC machining is both a tribute to the past and a glimpse into the future, where precision and quality will push mankind to new heights in industry.