CNC machining is a prototyping technique that enables industrial equipment and tools to be controlled by pre-programmed software. This method is completely automated and does not need any human intervention.
Computer Numerical Control, or CNC, is a process that utilizes numerical data that has been entered into the machine and is controlled by a computer. CAD software is often used for this procedure; it enables manufacturers, designers, or users to create the appropriate product designs and then permits the computer to control the machining tools’ motions.
This procedure may be used to create prototypes of the final product or increase the volume of a product’s manufacturing. CNC machining enables the user to control various lathes and drills without human intervention.
Prototype plastic parts are essential engineering materials available today due to their flexibility and multiple advantages. BMW saved up to 100 kg by omitting metals from the rear boot lid and front wings of its 6-Series Coupe and replacing them with thermoplastics and composites. BMW could not have taken this daring move without developing prototypes and testing them.
Assume you’ve had a great idea and designed a new product or component. You should continue creating plastic prototypes using any machining, correct? Wrong! While BMW may not inform you, the success of your project is still heavily dependent on the machining process used to build these components and the third-party manufacturer you choose.
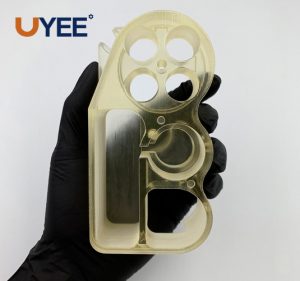
Rapidly and Efficiently Prototype Plastic Parts
Plastics have physical characteristics that make them an excellent material option for various applications. For instance, plastics are not conductors and generate less friction while also resistant to chemical pollutants. Plastics are affordable and lightweight, which helps projects stay within their budgets. This adaptability makes plastics an integral aspect of manufacturing globally and a critical component of prototyping novel products.
We may use plastic to prototype a metal item as a proof of concept or validate the part’s shape and fit. Rapid prototyping using plastic materials shortens the time required to design a new product and decreases costs. CNC machining services is routinely used to enhance prototype plastic components destined for injection molding in high-volume manufacturing. Because the iterative design cycle associated with product development is incompatible with the high initial injection molding expenses, engineers save time & expense by first machining their prototypes.
CNC Machining for Plastic Prototype
Plastic CNC precision machining is a technology that uses digital milling machines with three axes and software control to manufacture items from plastic materials.
CNC machining of plastic prototypes is known as the ‘Subtractive’ approach due to the prototype of material removal. Numerous thermoplastics are utilized in CNC machining services, including acrylic/plexiglass sheets, ABS, polycarbonate sheets, POM/Acetal, Teflon, and PEEK. The biggest aspect of this method is that it removes the need for molds, which saves time and money on production.
This approach is well-suited for prototypes with close tolerances and is the most adaptable and economical method for generating less than ten prototypes or models.
When Should We Use CNC Machining for Plastic Prototyping?
CNC machining is more adaptable and cost-effective than other rapid prototyping processes. CNC machining may outperform alternative prototyping techniques like 3D printing additive manufacturing in certain instances.
This technology’s extensive material selection and high tolerance capability may be the primary reason we should prioritize it above other rapid prototyping processes.
This rapid prototyping technique is well-suited for low-volume manufacturing and is affordable. Therefore, if you want a quick turnaround and want to produce a prototype free of extra materials and hidden costs, this is just what you require.
CNC machining offers various benefits, and the following are four instances when CNC plastic machining might be justified.
Scenario No. 1: The Design Features of Your Plastic Prototype Minor Particulars
Do you have a design that demands close tolerances and patterns with tiny radii? Then CNC machining is almost certainly the best option for your project. A CNC milling machine can produce radii as tiny as R0.05 mm and tolerances as close as 4 m.
Scenario No. 2: You Require a Superior Surface Finish
If you’re fabricating plastic prototypes purely to visualize thoughts or ideas, CNC machining is a good option. It produces a high-quality surface finish and does not leave the layer markings associated with 3D printing.
Scenario No. 3: You Wish to Work with a Unique Plastic Material
3D printing plastics and polymers such as PVC, PEI, POM, and PEEK. These and other plastics are suitable with a CNC machine shop. A machinist will have little difficulty constructing a CNC plastic prototype design, assuming that the plastic is available in blocks.
Scenario No. 4: You Require a Flexible and Rapid Machining Method
Are you interested in developing working plastic prototypes that you can test to identify design flaws? Because the CNC machine shop makes machined plastic prototypes using 3D CAD models and computer instructions, you can rapidly modify designs and conduct new testing on them.
Benefits of Plastic Prototyping With CNC Machining
SPEED
CNC machining is comparable to other rapid prototyping techniques such as 3D printing in terms of speed.
When numerical data is entered into computer software, the program will autonomously control the machining tools with little human intervention, significantly speeding up the operation.
QUALITY Product
Before mass manufacturing, it’s an excellent approach to ascertain the product’s shortcomings, advantages, and disadvantages.
CNC prototype machining enables the production of very high-quality components. They may be accurately manufactured to the required dimensions each time. It is vital to maintain uniformity in the goods’ quality as one must be similar to the others.
COST
If a product’s construction costs are high, end-consumers would pay a premium to purchase it. If the product’s price is too high, people will undoubtedly seek more cheap alternatives. You will almost certainly lose consumers.
CNC machining contributes to Plastic prototype cost savings. This procedure minimizes human participation and outperforms human equivalents, so you avoid paying labor costs, making it cost-effective.
TIGHTER TOLERANCE
CNC machining is an excellent alternative for products that need a +/-.005 tolerance. It is because it may jeopardize the tight tolerance measurement indefinitely.
This technique is used to fabricate very precise industrial components.
GREATER RESISTANCE
In terms of resistance, plastic components manufactured using CNC machining services outperform metal components. Metal components may rust over time, but plastic components are more rust-resistant and durable.
ADAPTABILITY
CNC machined plastic components are created directly from thermoplastic sheets or blocks using pre-programmed software. It enables a designer or engineer to make minor adjustments to the digital design between recurrences.
Because it does not need new tooling for adjustments, only a little expense is required for component upgrades.
MOLD-FREE
One of the compelling benefits of CNC machining is that it is completely mold-free. It is efficient at producing pieces without molds or other support structures; this is particularly useful for prototypes and low-volume manufacturing.
The costliest component of injection molding is creating metal tolling. However, this step is unnecessary with plastic machining.
Plastic Materials for CNC Machining: A Detailed Guide
Thermoplastic polymers used in CNC plastic machining are the following:
- ABS
- PA (Nylon)
- Acrylic
- LDPE
- POM (Delrin)
- HDPE
- Teflon
- PBT
- PEEK
- PET
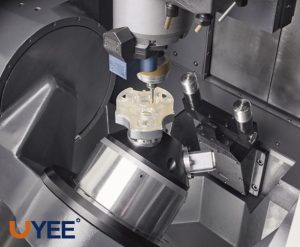
3 Steps for Creating Plastic CNC Machining Prototypes
- Concept Development
The first stage in this procedure is to bring a concept to life by sketching or writing it down on paper or another medium. This way, you’ll have a clear visual representation of the product prototype. After completing this step, you’ll better understand if any changes to the design are necessary.
- Creation of A Virtual Prototype
If you can create your prototype using 3d design technology, take it. It will aid you in envisioning the final look of your product and offer you a clear knowledge of how it will operate in light of its expectations. It is preferable to contract a professional prototype designer to create the virtual design.
- Construction of The Physical Prototype
After you’ve accomplished the first two processes, it’s time to continue to the final stage, developing the prototype’s physical structure.
After obtaining the correct shape, you should seek a mass manufacturing plastic prototype. Ensure that the final plastic prototype closely resembles the final product offered to consumers.
Bottom Line
We are a major manufacturer of precision components based in China. Our highly skilled experts will collaborate with you to develop high-quality prototypes utilizing advanced CNC precision machining, 3D printing, injection molding, and vacuum casting technologies. Please inform us about your prototyping project immediately and allow us to assist you in determining the most appropriate prototyping approach.