PLASTIC RAPID PROTOTYPING
Businesses and entrepreneurs benefit significantly from prototyping. It is a method for evaluating or presenting a physical product which is done by prototype manufacturer before mass manufacturing.
This skill is essential because it enables you to manipulate a physical representation of your product rapidly. It might also provide you the chance to pitch your concept to prospective investors. This would allow you to measure interest in your idea before its release. In this blog, you will learn how to start a plastic product development using Rapid prototype technology. Read on to know more!
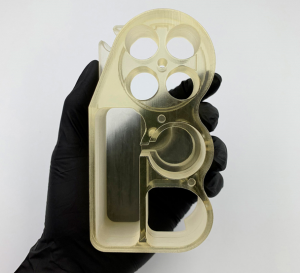
Bringing Ideas to Life
Prototyping is essential to the product development process. For instance, you may wish to take a product from idea through final construction. In this case, constructing a plastic prototype is a crucial step in the initial production process. With a plastic prototype, a design may be tested. Before developing a prototype, though, you must codify your project’s ideas.
This activity may be completed by developing or requesting a computer-aided design (CAD) model. It will demonstrate to you and the professional who will develop your prototype the desired appearance of your product.
The CAD model will also illustrate how the prototype’s components will fit together. Moreover, it will demonstrate how your product will operate as a complete.
Keeping this in mind, a company may assist you in developing either a functional or visual prototype. A visual prototype will show you how your final product will seem. In the meanwhile, a functioning prototype will offer a depiction of the entire product, from the materials to the mechanics.
There are four practical ways to produce a plastic prototype. These strategies include:
- Rapid tooling
- Urethane casting
- Stereolithography
- CNC plastic machining
The following entries provide a more in-depth examination of these distinct plastic prototype manufacturing techniques.
One More Step Before Prototype Building
Injection molding, the first plastic prototype manufacturing technology, required an additional step before making a product mockup. Before constructing a prototype, your design business must produce a mold, as its name indicates.
Rapid tooling for plastic injection is often used to generate plastic prototypes in the actual material. Using this strategy, the prototype development procedure is comparable to a complete production run.
However, it is quicker and simpler. In addition, the final product is not intended for long-term usage.
A prototyping company may utilize a joint mold base and aluminum to produce the mold. These materials allow the fabrication company to cut expenses and production time for your prototype.
The cost and time required to build your prototype mold will ultimately vary depending on the intricacy of your product. A fabricator may produce your prototype in as little as two to four weeks. In addition, the prototype will likely be 40% to 60% less expensive than a regular mold.
The fabricator will begin the procedure by analyzing your product thoroughly. Then, they will create a tooling plan for your mold. Once the mold is complete, they may make your prototype.
Rapid Outcomes Through Injection Molding Prototyping
Injection molding allows manufacturers to produce high-quality products rapidly. It is perfect for a short plastic prototype manufacturing run.
This strategy provides for rapid and cost-effective idea testing. For instance, an injection-molded prototype may provide light on your product’s mechanical functioning.
In addition, a prototype developed using this technique will enable you to examine all the necessary components. A plastic injection mold prototype allows you to experience a near-perfect reproduction of your final product in the real world. Several sectors use this strategy regularly. These sectors include:
- Automobiles
- Electronics
- Healthcare
- Packaging
Plastic injection molding functions effectively in industries that demand extensive testing and certification. One such area is the medical industry.
Benefits of Injection Molding
Prototyping using plastic injection molds allows fabricators to make high-precision, finely detailed prototypes. They can manufacture prototypes for objects weighing between a few grams and many kilos. In addition, they may employ the prototyping approach to build intricate forms.
With the suitable material, a plastic prototype has the same durability and mechanical qualities as the final product. Consequently, project owners may complete duties as required.
Even for their marketing initiatives, they might employ a plastic injection prototype. This prototype might be used for a limited production run in certain instances.
Vacuum Casting for High Precision
The following technique of plastic prototyping is vacuum casting. It is another technology for rapid prototyping that allows fabricators to copy hundreds of plastic pieces.
They would produce the components using a master model. The resultant parts are appropriate for fundamental testing.
This technique makes use of the vacuum effect. For this reason, you may also hear vacuum casting referred to as silicone molding.
A master model is necessary to create a silicone mold. Fabricators may use 3D machining or 3D printing to generate the master model. The 3D-printed item will next be used to construct the silicone mold.
The silicone mold may be reused by the fabricator several times. However, its service life is relatively short. During the mold’s service life, the fabricator may manufacture an exact duplicate of any component.
Benefits of Vacuum Casting
Casting allows fabricators to make high-precision, intricate plastic prototypes. A silicone mold reproduces prototype components similar to the final product.
This achievement is achievable even with intricate forms. These prototypes are flawless in every aspect. Even their quality is comparable to that of the final product.
With the proper mold material, your prototype may be as near as possible to the final product. There are several resources accessible.
The injection materials differ in flexibility, stiffness, and surface roughness. You may also paint them appropriately or build a translucent prototype like a crystal.
Create a Complex Plastic Prototype Using Stereolithography
Stereolithography is a practical approach for making single plastic prototypes. It allows fabricators to produce geometrically complicated forms.
Using this procedure, you may utilize a plastic prototype manufacturing to do a visual examination. This form of the prototype may also be used for marketing validation. You could even use it for ergonomic testing.
SLA is an additive plastic prototype design service. It is a precursor of 3D printing.
Fabricators create SLA plastic prototypes on demand. During the procedure, they apply consecutive layers of photosensitive resin.
The fabricator uses a machine to build layers. The device is computer-controlled. The computer will guide a UV laser to harden liquid material throughout the procedure.
For instance, certain resins are translucent. Others are resistant to water.
Yet some resins are less stiff. Despite this, there are restricted material options when employing SLA prototype plastic parts.
Benefits of Vacuum Stereolithography
SLA plastic prototyping is a high-precision technique for creating objects with intricate details. Using this technology, fabricators may make weak layers. Moreover, fabricators can produce incredibly realistic prototype finishes. Despite the resin usage, the plastic prototype’s functioning and surface quality will be comparable to the actual product’s.
The surface of SLA plastic prototypes is smooth. This approach is practical for modest to two-meter-long components. Regardless of the size of your product, SLA plastic prototyping will provide the same high-quality results.
CNC Plastic Prototype Machining
Our last plastic prototyping approach is CNC machining. Fabricators utilize a digital milling machine throughout this procedure. This plastic prototyping process is perfect for generating one-off components for functional testing.
In contrast to SLA plastic prototyping, CNC plastic prototype is a subtractive procedure. In other terms, it entails material removal.
Nevertheless, fabricators may employ CNC plastic prototyping with a variety of materials. This approach is efficient for creating ten or fewer prototypes.
Fabricators utilize a milling machine for this technique. A milling device has three digitally controlled axes.
A computer controls the operation of the machine. Using a 3D file, the computer will guide the device. The fabricators automate the whole process. CNC plastic prototyping differs somewhat from our other prototyping techniques. It does not need a mold.
It costs less, and you may get this project started more quickly. A CAD rendering is all that is required to get started with CNC plastic prototyping.
Benefits of CNC Machine Prototyping
Again, a large variety of materials are suitable for machine prototyping. Consequently, this strategy simplifies locating the appropriate materials for a specific project.
The mechanical qualities of the final plastic prototype will be comparable to those of an injection-molded product. However, this result differs based on your product’s usefulness and visual appeal.
You may, for instance, elect to refine your completed prototype. Additionally, you could paint your prototype in whatever color you desire.
Bottom Line
We can say that rapid prototyping may provide a significant competitive edge if you make products. Your prototype’s quality can only be as good as your fabricator’s. Our company specializes in rapid prototyping services and premium finishing.
Rapid prototyping becomes essential because a company’s success depends on speedier product development and technological innovation. You will have simple access to this service with us. Our specialists are professionals in digital modeling. Additionally, we provide the most innovative prototyping technology in China. Get in touch with us in case of queries. Our experts are always ready to serve you with the most cutting-edge services.
SEND US AN INQUIRY